En ocasiones uno se encuentra con que, para armar un prototipo o algún dispositivo único (no en gran escala de producción) es necesario soldar un componente con encapsulado QFN. Este integrado no tiene “patitas”. Su forma típica es la que se muestra en la figura:
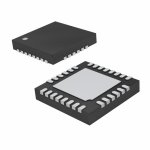
Cuando se quiere armar un impreso “casero” con un encapsulado como este el soldado manual se complica. Mas que nada porque los integrados suelen ser pequeños y tener un ancho de pista menor a la centésima de pulgada. Industrialmente estos encapsulados se sueldan sumergiendo la plaqueta en un baño de estaño fundido o bien con aire caliente.
Personalmente me ha tocado soldar de estos integrados con los elementos comunes que contamos los hobbystas (soldador , plancha, flux, etc) y aquí coloco algunas pautas que he concluido como importantes y espero que a alguien le sirva.
1) Si el integrado posee un ancho de pad menor o igual a una centésima de pulgada (0.254 mm) y la separación de pads es de un valor cercano a este (caso general) es conveniente diseñar el pcb con pistas que tengan de 0.1 a 0.15 mm en lugar de 0.254 mm. Esto es, porque al pasarle la plancha a la plaqueta, cuando se quiere generar la máscara, la tinta se aplasta y aumenta su espesor, en la mayoría de los casos cortocircuitándose las pistas.
2) La mayoría de estos encapsulados suelen traer un pad térmico que es el que se ve en la figura anterior como un cuadrado metálico en el centro del integrado. En algunos casos este pad está conectado a la tierra del dispositivo interior y se usa para ayudar a disipar el calor en algunos integrados que manejan potencia. Para el soldado, este pad es muy útil, pues fija al integrado en la posición correcta antes de soldar las pistas.
3) Es importante que las pistas de cobre del pcb que salen del integrado, lo hagan de manera perpendicular a este y paralelas entre sí hasta al menos 5 mm del integrado. Mas mejor. Luego se puede desviar la pista a la dirección que sea conveniente. Este proceso será importante al momento del soldado de las pistas. Las figuras que vienen a continuación muestran esta tendencia.
Pasos previos al soldado:
Generar un plano de cobre apropiado para que se agarre el pad térmico a la placa. En este punto surgen dos formas de hacer el soldado del pad térmico, con el soldador o con la plancha. Ambas formas tienen sus ventajas y desventajas.
Si se va a soldar con soldador, el plano de cobre debe salir por fuera de la base del integrado, para poder apoyarle la punta del soldador y derretir el estaño que hay por debajo del integrado. La siguiente imagen es un integrado convertidor DC-DC de Texas Instruments TPS63060:
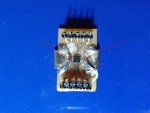
Las flechas marcan como el plano de cobre del pad térmico sale por fuera del integrado. ACLARACIÓN: en este caso fue fácil sacar el plano afuera dado que el integrado solo cuenta con dos filas de pines. En otros casos, los cuatro lados tendrán pines y habrá que sacar el plano de cobre por las esquinas del integrado o bien, no sacar el plano de cobre afuera y utilizar la plancha para soldarlo.
Para soldar con la plancha, generar un plano cuadrado y apoyar la plaqueta sobre una plancha caliente invertida.
Ventajas de soldar con la plancha:
1) No nos complicamos con sacar el plano del pad térmico por las esquinas del integrado.
2) Tenemos las manos libres para alinear el integrado correctamente con una pinza de precisión.
Desventajas de soldar con la plancha:
1) No puede haber ningún otro componente en la plaqueta al momento del soldado. Puesto que se quemaría o impediría que la plaqueta haga buen contacto con la plancha.
2) Es probable que el integrado reciba demasiado calor si nos demoramos mucho en alinearlo. Puede dañarse.
3) La plaqueta suele quedar con un color mas oscuro. Debido al calor intenso recibido.
Ventajas de soldar con soldador:
1) Cuidamos mas al integrado del calor.
Desventajas de soldar con soldador:
1) Nos queda ocupada una mano, con la otra debemos alinear el componente como podamos.
Como se vio en la imagen anterior, es útil fabricarle un “nuevo” encapsulado al integrado, soldandolo a una pequeña plaquetita con headers para utilizarlo como si fuera un encapsulado PDIP.
La siguiente imagen es un microcontrolador de Freescale que pedí por error como muestra con encapsulado QFN, cuando había disponibles encapsulados mas amigables. Este está soldado con plancha:
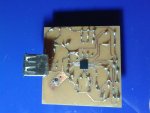
Y el mas chico que soldé es un acelerómetro de Freescale, tiene 3 mm de ancho:
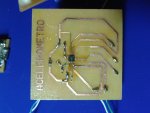
Flux, bendito seas:
Es muy importante colocar flux tanto en la plaqueta como en el integrado. Si bien es algo que se usa siempre, en el caso de encapsulados QFN es imprescindible.
Dejar secar bien el flux antes de soldar. Al componente conviene colocarle el flux con un palito o pincel y no rociarlo con el aerosol.
Soldado:
Sin colocar el componente todavía y con flux en la plaqueta, estañar solamente el plano térmico (no las pistas).
Acomodar el integrado aproximadamente en su posición correcta. Calentar el plano térmico ya sea con la plancha o con el soldador y tratar de alinear el integrado con una pinza. No es muy difícil. Una cosa extraña que me pasó con el TPS63060 fue que al calentar el estaño y al ser tan liviano el integrado, este se alineó solo automáticamente (estaba aproximadamente centrado antes) . No se porque será, ¿casualidad? ¿Tendrá que ver con la tensión superficial del líquido?
Se puede chequear que el integrado haya quedado alineado con alguna luz brillante. Se debe ver brillar el pad justo arriba de la pista.
Una vez que el componente está en su posición correcta hay que soldar las pistas. Como se dijo previamente, es conveniente que las pistas tengan cierto recorrido al salir del integrado sin cambiar de dirección.
Para soldar las pistas se hace lado por lado. Para cada lado apoyar el soldador contra el integrado y agregar bastante estaño. Mientras el estaño esté fundido, se verá que las pistas están cortocircuitadas, pero esto no es problema porque luego se comienza a “peinar” el estaño hacia fuera del integrado siguiendo la trayectoria de las pistas. Y el estaño solo quedará en las pistas y en los pads del integrado:
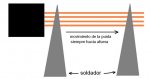
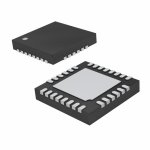
Cuando se quiere armar un impreso “casero” con un encapsulado como este el soldado manual se complica. Mas que nada porque los integrados suelen ser pequeños y tener un ancho de pista menor a la centésima de pulgada. Industrialmente estos encapsulados se sueldan sumergiendo la plaqueta en un baño de estaño fundido o bien con aire caliente.
Personalmente me ha tocado soldar de estos integrados con los elementos comunes que contamos los hobbystas (soldador , plancha, flux, etc) y aquí coloco algunas pautas que he concluido como importantes y espero que a alguien le sirva.
1) Si el integrado posee un ancho de pad menor o igual a una centésima de pulgada (0.254 mm) y la separación de pads es de un valor cercano a este (caso general) es conveniente diseñar el pcb con pistas que tengan de 0.1 a 0.15 mm en lugar de 0.254 mm. Esto es, porque al pasarle la plancha a la plaqueta, cuando se quiere generar la máscara, la tinta se aplasta y aumenta su espesor, en la mayoría de los casos cortocircuitándose las pistas.
2) La mayoría de estos encapsulados suelen traer un pad térmico que es el que se ve en la figura anterior como un cuadrado metálico en el centro del integrado. En algunos casos este pad está conectado a la tierra del dispositivo interior y se usa para ayudar a disipar el calor en algunos integrados que manejan potencia. Para el soldado, este pad es muy útil, pues fija al integrado en la posición correcta antes de soldar las pistas.
3) Es importante que las pistas de cobre del pcb que salen del integrado, lo hagan de manera perpendicular a este y paralelas entre sí hasta al menos 5 mm del integrado. Mas mejor. Luego se puede desviar la pista a la dirección que sea conveniente. Este proceso será importante al momento del soldado de las pistas. Las figuras que vienen a continuación muestran esta tendencia.
Pasos previos al soldado:
Generar un plano de cobre apropiado para que se agarre el pad térmico a la placa. En este punto surgen dos formas de hacer el soldado del pad térmico, con el soldador o con la plancha. Ambas formas tienen sus ventajas y desventajas.
Si se va a soldar con soldador, el plano de cobre debe salir por fuera de la base del integrado, para poder apoyarle la punta del soldador y derretir el estaño que hay por debajo del integrado. La siguiente imagen es un integrado convertidor DC-DC de Texas Instruments TPS63060:
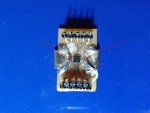
Las flechas marcan como el plano de cobre del pad térmico sale por fuera del integrado. ACLARACIÓN: en este caso fue fácil sacar el plano afuera dado que el integrado solo cuenta con dos filas de pines. En otros casos, los cuatro lados tendrán pines y habrá que sacar el plano de cobre por las esquinas del integrado o bien, no sacar el plano de cobre afuera y utilizar la plancha para soldarlo.
Para soldar con la plancha, generar un plano cuadrado y apoyar la plaqueta sobre una plancha caliente invertida.
Ventajas de soldar con la plancha:
1) No nos complicamos con sacar el plano del pad térmico por las esquinas del integrado.
2) Tenemos las manos libres para alinear el integrado correctamente con una pinza de precisión.
Desventajas de soldar con la plancha:
1) No puede haber ningún otro componente en la plaqueta al momento del soldado. Puesto que se quemaría o impediría que la plaqueta haga buen contacto con la plancha.
2) Es probable que el integrado reciba demasiado calor si nos demoramos mucho en alinearlo. Puede dañarse.
3) La plaqueta suele quedar con un color mas oscuro. Debido al calor intenso recibido.
Ventajas de soldar con soldador:
1) Cuidamos mas al integrado del calor.
Desventajas de soldar con soldador:
1) Nos queda ocupada una mano, con la otra debemos alinear el componente como podamos.
Como se vio en la imagen anterior, es útil fabricarle un “nuevo” encapsulado al integrado, soldandolo a una pequeña plaquetita con headers para utilizarlo como si fuera un encapsulado PDIP.
La siguiente imagen es un microcontrolador de Freescale que pedí por error como muestra con encapsulado QFN, cuando había disponibles encapsulados mas amigables. Este está soldado con plancha:
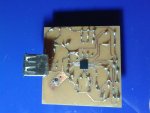
Y el mas chico que soldé es un acelerómetro de Freescale, tiene 3 mm de ancho:
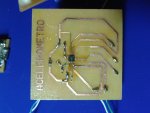
Flux, bendito seas:
Es muy importante colocar flux tanto en la plaqueta como en el integrado. Si bien es algo que se usa siempre, en el caso de encapsulados QFN es imprescindible.
Dejar secar bien el flux antes de soldar. Al componente conviene colocarle el flux con un palito o pincel y no rociarlo con el aerosol.
Soldado:
Sin colocar el componente todavía y con flux en la plaqueta, estañar solamente el plano térmico (no las pistas).
Acomodar el integrado aproximadamente en su posición correcta. Calentar el plano térmico ya sea con la plancha o con el soldador y tratar de alinear el integrado con una pinza. No es muy difícil. Una cosa extraña que me pasó con el TPS63060 fue que al calentar el estaño y al ser tan liviano el integrado, este se alineó solo automáticamente (estaba aproximadamente centrado antes) . No se porque será, ¿casualidad? ¿Tendrá que ver con la tensión superficial del líquido?
Se puede chequear que el integrado haya quedado alineado con alguna luz brillante. Se debe ver brillar el pad justo arriba de la pista.
Una vez que el componente está en su posición correcta hay que soldar las pistas. Como se dijo previamente, es conveniente que las pistas tengan cierto recorrido al salir del integrado sin cambiar de dirección.
Para soldar las pistas se hace lado por lado. Para cada lado apoyar el soldador contra el integrado y agregar bastante estaño. Mientras el estaño esté fundido, se verá que las pistas están cortocircuitadas, pero esto no es problema porque luego se comienza a “peinar” el estaño hacia fuera del integrado siguiendo la trayectoria de las pistas. Y el estaño solo quedará en las pistas y en los pads del integrado:
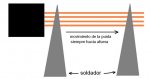